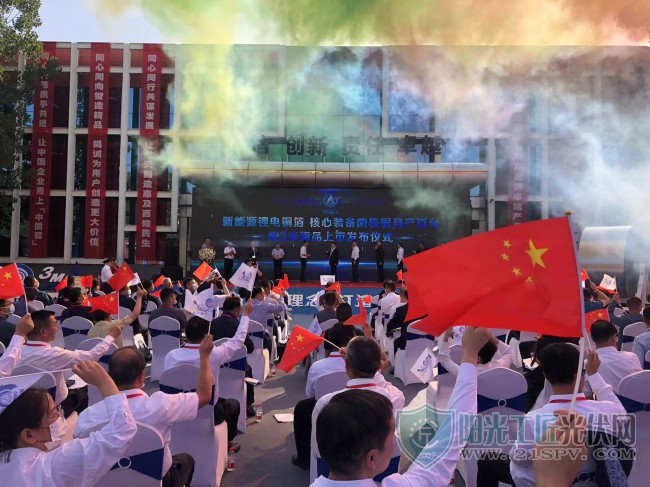
新能源汽車(chē)、數(shù)碼產(chǎn)品、儲(chǔ)能設(shè)備的發(fā)展核心在于電池技術(shù),而鋰電銅箔正是鋰電池的重要材料之一。陰極輥?zhàn)鳛殂~箔生產(chǎn)的核心設(shè)備,其規(guī)格尺寸、導(dǎo)電能力、晶粒大小,都涉及銅箔的生產(chǎn)效率、經(jīng)濟(jì)效益和產(chǎn)品質(zhì)量,一直以來(lái)都是銅箔企業(yè)關(guān)注的核心和焦點(diǎn)。
我國(guó)鋰電銅箔的生產(chǎn)設(shè)備陰極輥長(zhǎng)期被外企壟斷,嚴(yán)重制約著國(guó)產(chǎn)新能源電動(dòng)汽車(chē)、數(shù)碼產(chǎn)品、儲(chǔ)能設(shè)備的發(fā)展。中國(guó)大直徑陰極輥的研制與生產(chǎn)相繼經(jīng)歷了1.5、2.0、2.7和3.0幾個(gè)歷程,先后攻克了大直徑陰極輥的材料成形、結(jié)構(gòu)優(yōu)化、鈦筒旋壓、熱裝等多項(xiàng)核心技術(shù)。2016年,首件直徑2.7米的金屬鈦筒旋壓成型成功,國(guó)內(nèi)首臺(tái)擁有完全自主知識(shí)產(chǎn)權(quán)的直徑2.7米陰極輥在陜西順利下線;2020年航天四院研制出2.7米“新一代高精度進(jìn)口替代陰極輥”,不僅使鈦筒晶粒度從此前的7-8級(jí)全部提高到10級(jí)以上,鈦筒內(nèi)部組織致密性、電流密度均勻性和導(dǎo)電能力也大幅提高,生箔質(zhì)量顯著提升。“3.0m大規(guī)格高精度陰極輥”成功研制出,可生產(chǎn)效率同比提高13%、能耗相對(duì)降低3%,晶粒度超過(guò)10級(jí),電流超過(guò)6萬(wàn)安培,導(dǎo)電更均勻、品質(zhì)更穩(wěn)定,性?xún)r(jià)比更高,必將為用戶創(chuàng)造更高價(jià)值。
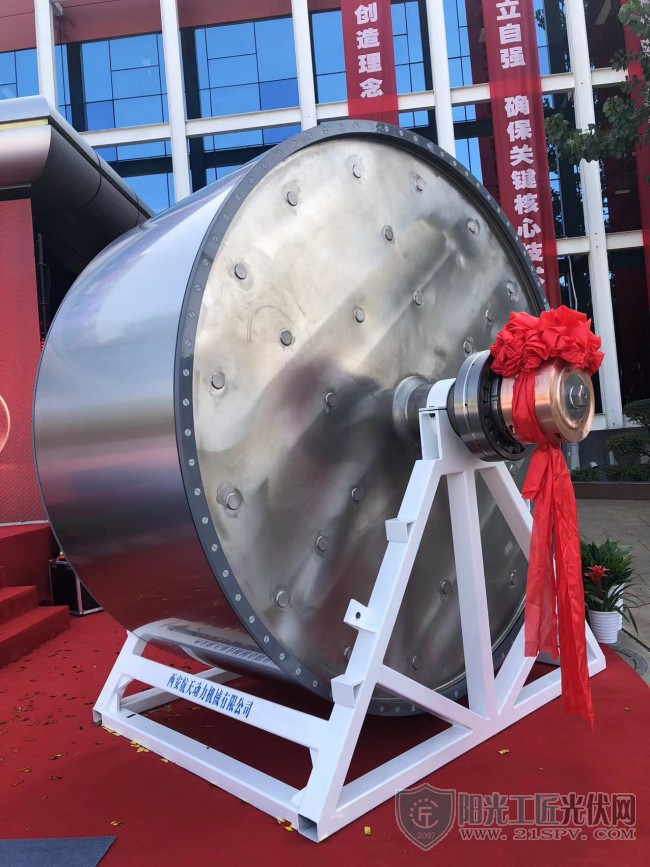
據(jù)航天科技集團(tuán)四院院長(zhǎng)助理李樹(shù)海介紹,四院依托航天固體火箭發(fā)動(dòng)機(jī)金屬殼體旋壓設(shè)備和金屬圓筒無(wú)縫旋壓成形工藝等技術(shù)優(yōu)勢(shì),將陰極輥制造逐步培育成企業(yè)重要的民用產(chǎn)業(yè)項(xiàng)目。相繼與原材料冶煉鍛造企業(yè)和行業(yè)專(zhuān)家,以及西安交大、西工大等高校聯(lián)合開(kāi)展技術(shù)攻關(guān),采用無(wú)縫旋壓成形鈦筒技術(shù)及特殊工藝制造的陰極輥,相較于國(guó)外企業(yè)采用卷焊成形鈦筒技術(shù)制造的陰極輥,其最大優(yōu)勢(shì)就是鈦筒厚度大、壽命長(zhǎng),生產(chǎn)出的箔面無(wú)壓痕、無(wú)亮帶,銅箔品相更好。自2016年下半年至2022年上半年,為國(guó)內(nèi)50余家銅箔生產(chǎn)企業(yè)生產(chǎn)制造了各種規(guī)格的陰極輥達(dá)上千臺(tái),累計(jì)簽訂合同近50億元,產(chǎn)品國(guó)內(nèi)市場(chǎng)占有率達(dá)70%以上。
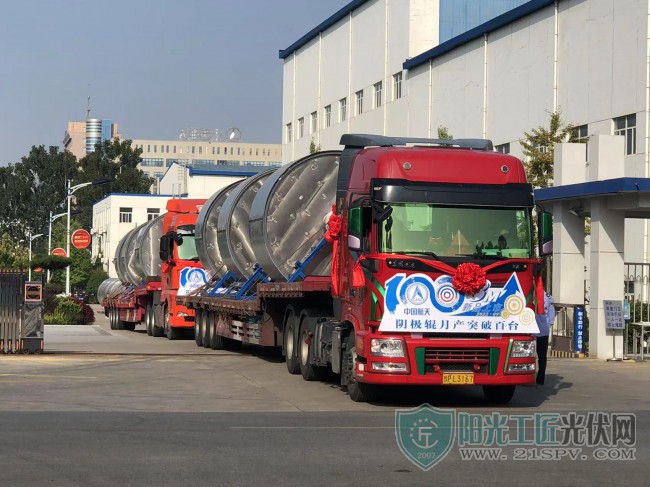
原標(biāo)題:我國(guó)超大直徑陰極輥制造技術(shù)實(shí)現(xiàn)了重大突破