在動力電池起初的發(fā)展階段,磷酸鐵鋰電池由于其非常高的安全性能受到整車廠及消費者的青睞。
然而,在現(xiàn)有的政策體系下,磷酸鐵鋰的能量密度已經達不到要求,必須發(fā)展更高能量密度的體系。本文主要探究300 W·h/kg單體電池及相應系統(tǒng)的開發(fā)。
01、正極材料
開發(fā)鋰離子電池動力電池用高容量正極材料,是解決電動車輛用長壽命、安全型、低成本的高能量密度鋰離子動力電池的關鍵。在諸多正極材料中,高鎳材料由于其高比容量特性而備受關注(圖1)。
國外比較先進的企業(yè),如松下和LG化學,已經實現(xiàn)基于高鎳NCA和 NMC811材料的電池的商業(yè)化應用。
而國內的電池企業(yè),如比亞迪、寧德時代,在它們的技術路線規(guī)劃中,也已將高鎳NCM材料作為實現(xiàn)未來高比能量動力電池的正極材料。
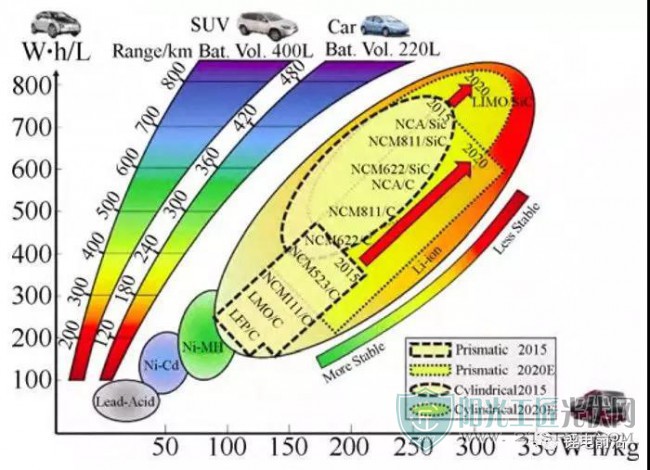
圖1 不同材料體系的能量密度及電動車續(xù)航里程對比
要想實現(xiàn)單體電池能量密度達到300W·h/kg,正極材料的克容量需要達到210mA·h/g以上。 為了獲得如此高容量的正極材料,高鎳材料中的鎳含量一般要達到85% (摩爾比)。然而隨著材料中鎳含量的增加,其結構穩(wěn)定性與熱穩(wěn)定性會大幅降低,如圖2所示。鎳含量較高的材料,在釋放高比容量的同時,其充電狀態(tài)下能脫出更多的鋰離子,因而產生大量的亞穩(wěn)態(tài) Ni4+。
這些高價態(tài)的鎳離子具有強烈的氧化性,會引發(fā)電極/電解液界面處的副反應。溫度升高時,這些副反應更加明顯。
此外,Ni4+還原后的二價鎳離子易與鋰離子發(fā)生鋰鎳混排現(xiàn)象而進入鋰層。這一過渡金屬向鋰層的遷移行為,誘導了層狀結構-尖晶石-巖鹽相的結構轉變,并貫穿整個循環(huán)過程,使電池性能劣化。
除此之外,材料鎳組分高,表面殘堿度高,吸水性很強,易與空氣中水分、二氧化碳等發(fā)生不可逆的反應,直接影響材料的存儲性能、加工性能和克容量性能的發(fā)揮。

圖2 不同 Ni含量三元材料的容量、循環(huán)及熱穩(wěn)定性關系圖
為了克服這些問題,研發(fā)人員采用多種陰、陽離子進行體相摻雜,來提升高鎳材料中陰陽離子結合鍵能,以穩(wěn)定材料結構,達到提升循環(huán)及存儲性能的效果。 例如,向NCA中摻雜Mg制得的 LiNi0.75Co0.15Al0.05Mg0.05O2,Ni、Li混排現(xiàn)象減少,材料層狀結構得到穩(wěn)定,循環(huán)過程中的相態(tài)變化得到抑制,阻抗降低,常溫和高溫下NCA材料的循環(huán)性能提升明顯。
此外,對材料進行表面包覆也是一種防止電解液對正極材料腐蝕、抑制副反應發(fā)生、提升材料循環(huán)及存儲穩(wěn)定性的有效方法。氟化物的改性效果較為明顯。
例如,AlF3包覆高鎳三元材料后其以1C在3.0——4.2V循環(huán)1000次,容量保持率仍有86.2%。從產業(yè)化方面來說,日韓企業(yè)尤其是日本的企業(yè)走在了NCA高鎳正極材料產業(yè)化的前列。
例如,日本化學產業(yè)株式會社、戶田化學(Toda)和住友金屬(Sumitomo)是NCA材料的主要供應商,而韓國的Ecopro、L&F及GSEM也有產品銷售。國內方面,目前也已有多家企業(yè)通過自身研發(fā)或者直接引入日韓技術,大力推進NCA的產業(yè)化進程,如當升科技、長遠鋰科、深圳貝特瑞等。
除了NCA材料外,NCM材料近年來也在國內外掀起了一股熱潮,如韓國的LG公司,其高鎳的NCM產品已經量產。國內企業(yè)如寧波金和、廈門鎢業(yè)、湖南瑞翔等也已經小批量生產高鎳NCM材料。
目前高鎳材料主要通過氫氧化物前驅體與鋰鹽反應制備,而氫氧化物前驅體采用共沉淀法制備。與常規(guī)三元材料不同的是,高鎳材料由于需要維持較高比例的Ni3+,因此燒結需要純氧氣氛。
此外,由于Ni3+在高溫下易發(fā)生歧化反應,因此燒結溫度 一般低于800℃,這就要求鋰源需要采用低熔點的氫氧化鋰。
另外,為了使氧氣進行更好地擴散,高鎳三元材料燒結時的裝缽量也低于常規(guī)三元材料。同時,高鎳材料制備對燒結窯爐密封性的要求、對車間環(huán)境(水分、溫度等)的要求都比較高,這也是其產業(yè)化進程相對較慢的一個原因。
為了滿足科技部重大專項對高鎳正極材料的需求,國軒高科及項目參與單位目前通過前驅體的優(yōu)化控制合成及后續(xù)的摻雜及包覆改性,制備出了0.2C克容量大于220mA·h/g的材料,材料首次充放電效率高達95%,1C循環(huán)50周容量保持率大于95%。
此外,面對當下應用需求,國軒高科還制備了容量略低(210 mA·h/g, 0.2 C)但是循環(huán)穩(wěn)定性更好(98%@50th)的三元材料,目前已用于全電池測試。目前使用自制的高鎳材料匹配石墨負極制備的能量密度 250 W·h/kg的軟包全電池1C循環(huán)超過1500周。
02、負極材料
在鋰離子電池負極材料方面,硅被認為是最有潛力的新一代高容量鋰離子電池負極材料。與傳統(tǒng)的石墨負極材料相比,硅具有極高的質量比容量(理論比容量高達4200mA·h/g)。
針對電池單體能量密度達到300W·h/kg的要求,負極材料主要采用高性能氧化亞硅/碳復合負極材料,復合材料的比容量必須高于600 mA·h/g。
但氧化亞硅/碳材料在使用過程中面臨首次庫侖效率低、循環(huán)性能差、體積膨脹大、導電性差等技術難題,必須從氧化亞硅、碳材料及二者的復合工藝、黏結劑以及電解液等多方面進行綜合改進。
2.1 研究內容
(1)高性能硅基負極材料的研發(fā)
重點研究容量較高、循環(huán)性能較好的氧化亞硅負極材料,包括:
① 氧化亞硅材料界面反應機理研究。分析氧化亞硅材料表面鍵型、結構演變與電解 液反應、黏結劑固化、電子和鋰子遷移動力學之間 的關系,探索穩(wěn)定氧化亞硅材料結構和 SEI 膜的表 面修飾方法;
② 氧化亞硅的合成工藝。研究宏量制備氧化亞硅材料的新工藝,兼顧產能、批量穩(wěn)定性以及材料成本。尤其是減少氧化亞硅顆粒的表面不 可逆消耗鋰源的硅氧烷鍵(≡≡Si—O—Si≡≡)和硅烷醇基(Si—OH)的生成量,提升氧化亞硅粉材料的 可逆容量和首次庫侖效率。
(2)硅/碳復合材料的研發(fā)
硅碳復合材料的目的是將碳材料的導電性和硅材料的高容量結合起來,進而充分發(fā)揮硅材料的電化學性能。包括:
① 硅/碳結構設計。將氧化亞硅和硬碳、石墨烯、納米碳管和石墨等不同碳材料復合,研究硅/碳之間的物理和化學復合機制;
② 硅/ 碳協(xié)同作用研究。研究碳種類、復合機制對于硅表面反應、電子和離子動力學行為的影響,通過對氧化亞硅材料表面進行碳復合,不僅增強電子傳導性, 而且避免硅基體材料和電解液直接接觸,對材料首次庫侖效率提升和后期循環(huán)穩(wěn)定性有利;
③ 在硅碳復合負極材料與高容量正極材料組成的全電池中,研究正極材料中溶解的金屬離子在硅碳負極上的沉積行為,及其對硅碳負極電化學性能的影響。
(3)硅基負極材料的黏結劑開發(fā)
通過對聚合物側基優(yōu)選和結構組成優(yōu)化,結合聚合物溶度參數、粘結強度與電化學性能之間的關聯(lián),合成具有高彈性的聚丙烯酸類水性黏結劑,研究乳膠粒子兩親性結構調控,優(yōu)化黏結劑對硅基負極材料的粘結強度以及對銅箔的附著力,從而提高硅基材料的電化學性能。
2.2 相關工藝
氧化亞硅材料除首次庫侖效率偏低外,其電子導電性也較差。因此在實際應用中,為降低材料極化,充分發(fā)揮材料的性能,需要對SiO進行碳包覆。相關工藝包括:
① 采用特定碳源包覆及特定的燒結工藝,減少氧化亞硅顆粒的表面氧化和氮化,以及材料中不可逆消耗鋰源的硅氧烷鍵和硅烷醇基生成量,一方面增強氧化亞硅材料電子傳導,同時避免硅基體材料和電解液直接接觸,提升其可逆容量、首次庫侖效率和消耗穩(wěn)定性;
② 在分子、納米/微米多尺度水平上調控硅/碳材料內部結構和表面形態(tài),分析材料微納米結構與宏觀性能的本質聯(lián)系,從而實現(xiàn)其電化學特性的改善和提高,研究結構不僅能夠指導對氧化亞硅/碳負極材料進行改善,而且可以為負極黏結劑和電解液的選擇提供參考;
③ 綜合運用石墨改性技術和超容量硬碳技術,制得與氧化亞硅材料最匹配的碳材料,進而改善氧化亞硅/ 碳材料的綜合性能。
目前國內外SiO/C材料的供應商對SiO包覆改 性主要集中在軟、硬碳包覆,如瀝青熱解、有機物熱解、CVD 包覆等。部分供應商針對碳包覆后的樣品進行二次聚合物包覆,從而提高氧化亞硅材料的循環(huán)穩(wěn)定性。
2.3 產業(yè)化現(xiàn)狀
相對于Si/C負極來說,SiOx/C負極因自身具有緩沖機制和體積膨脹率較小,因此更受商業(yè)應用的青睞。
日、韓企業(yè)在SiOx方面申請了較多的專利,其中信越化學公司的專利主要是關于SiOx有機氣體包覆、碳納米管復合以及預鋰化,大阪鈦的專利 主要是關于CVD和噴霧干燥包覆SiOx。
目前國外只有日本信越、大阪鈦業(yè)等公司的 SiOx在工業(yè)中小批量應用,無定形的硅合金材料和納米硅碳復合材料剛開始批量試制和評價。
國內對硅碳負極的研究主要集中在納米材料的合金化、碳復合、形貌調控等方面,取得了一定進展,但仍落后于日本等國家。相關電池材料企業(yè)也加大了對硅基負極材料的研發(fā),如深圳貝特瑞研發(fā)的氧化亞硅負極材料實現(xiàn)了氧化亞硅顆粒表層的均勻碳包覆,且已小規(guī)模量產。然而,動力電池用硅基負極材料的循環(huán)性能仍需進一步提高。
03、電解液
鋰離子電池電解液為離子電池的“血液”,它浸潤在正、負極極片、隔膜以及電池殼體之間的空隙中,主要起到離子導通的作用。
如前文所述,為了實現(xiàn)300 W·h/kg高能量密度電池體系,我們需要使用高鎳三元正極匹配硅基負極。然而,高容量的正極或者負極不可避免地對電解液提出更高的要求。為了應對挑戰(zhàn),一般情況下是往電解液中添加添加劑。
本小節(jié)度電將從正極成膜添加劑和負極成膜添加劑兩個維度來闡述高能量密池體系中電解液的相關信息。
3.1 正極成膜添加劑
高鎳三元正極材料克容量和電壓平臺較高,從電解液的角度來看面臨兩個需要解決的重要問題:
① 電解液很容易在高活性的高鎳三元正極材料材料表面氧化分解并釋放有害氣體;
② 高鎳正極材料本身結構不穩(wěn)定,在電解液中金屬離子容易溶出并 在負極表面還原沉積,造成不可逆容量衰減。
為了解決這些問題,一個重要途徑是往電解液中添加正極成膜添加劑,其可以優(yōu)于 EC、EMC 等溶劑在電池正極表面被氧化分解,形成正極SEI膜,抑制電解液與正極的副反應以及金屬離子溶出現(xiàn)象。常用的正極成膜保護劑包括硫系、磷系化合物。
例如,1,3-丙烯磺酸內酯(PES)已經被證明在三元/石墨電池體系中可以明顯提升電池的循環(huán)性能。另兩種硫系添加劑硫酸乙烯酯 DTD和甲烷二磺酸亞甲酯MMDS作為正極膜保護劑時,可以明顯降低三元材料表面成膜阻抗,提高充放電的庫侖效率。
此外,磷系添加劑亞磷酸三(三甲基硅)酯TTSPi也被證明可以在三元材料表面被選擇性地氧化形成穩(wěn)定的SEI膜,有效抑制金屬離子的溶出,提升三元電池的循環(huán)和倍率性能。雙草酸硼酸鋰LiBOB和二氟草 酸硼酸鋰LiODFB也可以在三元正極材料表面氧化成膜,缺點是 LiBOB的成膜阻抗較高,增加電池的內阻。
3.2 負極成膜添加劑
硅基材料在充放電循環(huán)過程中體積變化巨大,導致材料結構粉化,原有的導電網絡結構遭到破壞。此外,電解液不斷消耗形成新的SEI膜,最終結果是電池容量衰減很快、循環(huán)性能很差。
應用傳統(tǒng)的石墨負極成膜添加劑-碳酸亞乙烯酯(VC)可以有效地緩解這個問題。由于VC含有不飽和雙鍵,可以在硅基負極表面優(yōu)于普通的碳酸酯類溶劑被還原,形成具有一定柔性的聚碳酸酯類化合物,亦即柔性SEI膜。這種柔性膜在負極循環(huán)膨脹收縮的過程中不受破壞,因而有效提高了硅基負極的循環(huán)穩(wěn)定性。
除了VC,氟代碳酸亞乙烯酯(FEC)也被證明是優(yōu)異的硅基負極成膜添加劑。當電解液中不含F(xiàn)EC時,在硅基負極表面形成的SEI膜主要由不穩(wěn)定的Si—C以及Si—O鍵組成,在硅基負極的 體積膨脹過程中這些化學鍵很容易斷裂。
然而FEC的加入可以使得SEI膜中含有更穩(wěn)定的Si—F鍵,有效提高了SEI膜結構的致密性和穩(wěn)定性。FEC 的添加劑量對其應用性能影響很大,通常認為5%——10%含量的FEC對硅基負極性能的優(yōu)化提升效果最好,過多FEC的加入會因為氧化分解在SEI膜中產生更多不良鋰離子導體材料LiF,造成首效率降低和倍率性能下降。
在實際應用中,我們通常會加入VC與FEC的混合添加劑,通過兩者之間的協(xié)同效應,提升硅基負極電池的綜合性能。
除了常見的VC以及FEC添加劑以外,酸酐類添加劑、多氟代的碳酸酯類添加劑等也都被嘗試應用于硅基負極電池性能的提升。
需要注意的是,電解液配方組成尤其是添加劑的不同只能從離子遷移率、SEI膜修復等側面角度對全電池的綜合性能進行優(yōu)化提升,其不可能從根本上完全彌補現(xiàn)有正、負極材料的本征缺陷。在開發(fā)高比能電池體系中的高鎳三元材料以及硅基負極材料時,也需要同時考慮提高材料的結構穩(wěn)定性以 及與電解液的兼容性。
04、隔膜
4.1 隔膜性能要求
鋰離子電池隔膜的主要作用除了阻隔正負極,防止兩極接觸而短路外還可以提供鋰離子傳輸的通道。鋰離子電池對隔膜的基本要求:
① 隔膜對電解液和電極材料要有足夠的化學穩(wěn)定性,由于鋰離子電池電解液為強極性的有機化合物,因此隔膜必須耐電解液腐蝕,與正負極接觸時不發(fā)生反應;
② 隔膜要有良好的電化學穩(wěn)定性,因為鋰離子電池使用過程中的最高電壓可達到 4.5 V,隔膜處于極強的氧化還原環(huán)境中必須要有一定的化學穩(wěn)定性;
③ 有高的離子電導率。通常要求離子電導率大于 10-3 S/cm;
④ 隔膜厚度要求。隔膜厚,強度高,抗刺穿能力強,但容量低;厚度薄,離子傳導性好,但隔膜過薄,其保液能力及電子絕緣性降低,對電池性能產生不利影響,一般厚度值要求值在25μm以下,另外隔膜厚度均勻性對電池的循環(huán)也尤為重要;
⑤ 有合適的孔隙率??紫堵视绊懕R盒阅埽h(huán)及安全性能,一般要求40%——50%之間;
⑥ 隔膜孔徑分布??讖酱螅裟︿囯x子的遷移阻力小, 但隔膜力學性能及電子絕緣性下降,易短路,孔徑小,增加電池內阻,另外孔徑分布不均,容易造成電極/電解液界面電流密度不均,商業(yè)化鋰電池隔膜的孔徑一般在0.03——0.12μm,最大孔徑與最小孔徑之差控制在在 0.01μm以內;
⑦ 透氣性要求,透氣率是指一定量的空氣在單位壓差下通過單位面積隔膜所需的時間,Gurley值一般要求 200——400s-1,隔膜的透氣主要跟隔膜厚度,孔隙率,孔徑大小及分 布等多種因素有關,在固定孔結構下,透氣率與電阻成正比關系;
⑧ 隔膜要有高的機械強度,一般要求鋰離子電池隔膜抗刺穿強度>11.8kgf/mm (1kgf=9.80665N);
⑨ 隔膜要有良好的浸潤性,隔膜與電解液之間有較好的的潤濕性;
⑩ 隔膜應具有良好的尺寸穩(wěn)定性,電解液浸潤或高溫時,隔膜保持平整,無褶皺及扭曲現(xiàn)象。
最后對動力鋰電池安全性能比較重要的是熱閉合性能,當電池過充或外部短路時,產生大量的熱將導致電池內部溫度迅速升高,當溫度升高到隔膜材料的熔點時,材料發(fā)生熔融,從而堵住微孔形成熱閉合,阻斷離子的繼續(xù)傳輸而形成斷路,起到保護電池的作用,一般PE的閉孔溫度為 125℃,PP為160℃左右。
而破膜溫度是指電池內部溫度升高到一定程度時造成隔膜破裂,從而造成電池短路,隔膜發(fā)生破裂時的溫度即為破膜溫度。
一般PE的斷裂溫度為139℃,PP為 162℃左右,一般動力電池要求隔膜具有較低的閉孔溫度,較高的破裂溫度。
4.2 隔膜種類
根據結構及組成的不同,鋰離子電池隔膜主要分為聚烯烴微孔膜,無紡布膜及無機復合隔膜。聚烯烴類隔膜,包括干法PP隔膜、濕法PE隔膜。
干法又稱延伸法,制備工藝包括:流延、退火、復合、拉伸、分層、分切。干法隔膜簡單無污染,且成本較低,但是孔徑及孔隙率較難控制,且TD方向的拉伸強度較低,不適用于高安全性隔膜;
而濕法又稱熱致相分離法,同步拉伸的濕法隔膜TD方向的拉伸強度更強,孔徑、孔隙率及厚度等物化性能更加均勻可控,適合大規(guī)模應用。但這聚烯烴類隔膜也同樣存在一些問題,耐高溫性能差等。
鑒于上述聚烯烴膜的局限性,無紡布膜優(yōu)勢在于具有可設計的孔結構,孔隙率高,保液性好的優(yōu)勢。但無紡布隔膜纖維直徑一般為10——20μm,而鋰離子電池隔膜的厚度一般要求為25μm以下,孔徑無法滿足要求,靜電紡絲技術可以制備出納米纖維,但是該技術起步較晚,生產效率低,成本低,因此沒有得到大規(guī)模應用。
無機復合隔膜是將超細無機顆粒與少量黏結劑粘結而成的多孔膜,常見無機顆粒有氧化鋁、氧化硅、氧化鈦等,黏結劑主要有PVDF、PAN等。
這種復合膜可以提高電解液的浸潤性,及電池安全性能,但是機械強度較低,無法滿足電池卷繞及組裝的要求,鑒于以上問題,目前采用陶瓷涂覆膜來改善,涂覆隔膜的優(yōu)勢:
① 可以改善電解液的浸潤性,提高電池的吸液、保液能力,從而提高電池的 安全性能;
② 可以提高電池耐熱性,從而大大提高電池的安全性能;
③ 可大大提高隔膜的耐氧化性,對PE濕法隔膜尤為明顯;
④ 可中和電解液中少量的HF 及其它雜質,防止電池脹氣。
4.3 高比能電池隔膜
為增加高比能電池的安全性能,本項目采用高安全性濕法涂覆隔膜作為高能量密度電芯隔膜,在涂覆陶瓷的基礎上又進行了涂膠(圖4),這樣既可以充分發(fā)揮純陶瓷隔膜的優(yōu)勢外,膠可以將正負極片粘結在一起,避免了鋰離子在嵌入,脫嵌過程中的“死區(qū)”,縮短了鋰離子的傳輸路徑,對于界面的改善具有重要意義。
另外,有效避免了電池在跌落,碰撞過程中造成的隔膜與極片的錯位現(xiàn)象,降低短路發(fā)生率,提高電池的安全性能,最后可以提高電池的加工性能,方便入殼,從而提高電池制作效率。
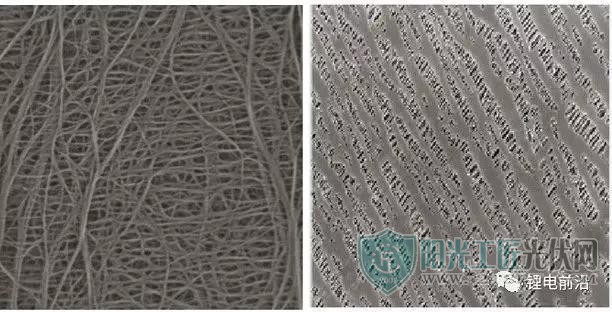
圖3 干法隔膜(左)、濕法隔膜(右)
高性能高安全的一些隔膜指標如下:高安全性:濕法涂覆隔膜涂層厚度達到2.5——6μm,涂層厚度偏差小于±5%, 其中無機耐高溫層厚度2——4μm,納米復合材料涂層厚度0.5——1μm;熱收縮:150℃,0.5h 下,MD方向熱收縮2%,TD方向熱收縮1%。 涂覆后的產品電解液潤濕能力提高50%以上;透氣性:涂覆后的產品透氣率增加不能超過原產品標準的20%,例如:
9μm的隔膜涂覆前透氣率標準為(210±50)s/100mL,
涂覆后產品的規(guī)格值為(240±50)s/100mL;
機械強度:MD拉伸強度1100 kgf/cm;
TD拉伸強度1100kgf/cm;
穿刺強度:500gf;
熱閉合性能,閉孔溫度:128℃,
破膜溫度:180℃;
水分含量:1000 ppm(1ppm=1X10-6 μg/g);
涂覆層的表面無明顯針眼,脫落,雜質等缺陷,表面粗糙度均一;
由隔膜制成的電池全部通過國際安全性測試;
電池熱復合后正極片與涂層的粘結強度30N/m(熱復合工藝:溫度70——100℃,壓力1——3 MPa,時間10——25s);
涂覆隔膜的克容量發(fā)揮99.5%(與對應的基膜相比)
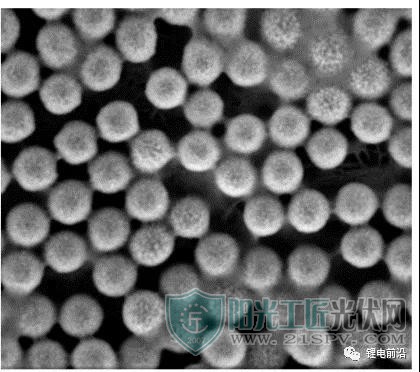
圖4 高安全性涂覆隔膜涂覆基膜面(a)、橫截面(b)
05、電池體系 5.1 封裝形式
目前,主流的封裝形式主要有三種,即圓柱、方形和軟包。不同的封裝結構意味著不同的特性,它們各有優(yōu)缺點。圓柱型鋰電池采用相當成熟的卷繞工藝,自動化程度高,產品傳品質穩(wěn)定,成本相對較低。
圓柱型鋰電池有諸多型號,比如常見的有14650、17490、18650、21700、26650等。圓柱型鋰電池在日本、韓國鋰電池企業(yè)中較為流行,中國國內也有相當規(guī)模的企業(yè)生產圓柱型鋰電池。
方形鋰電池通常是指鋁殼或鋼殼方形電池,方形電池的普及率在國內很高。國內動力電池廠商多 采用電池能量密度較高的鋁殼方形電池為主,因為方形電池的結構較為簡單,不像圓柱電池采用強度較高的不銹鋼作為殼體及具有防爆安全閥的等附件,所以整體附件重量要輕,相對能量密度較高。
但由于方形鋰電池可以根據產品的尺寸進行定制化生產,所以市場上有成千上萬種型號,而正因為型號太多,工藝很難統(tǒng)一。
軟包鋰電池使用軟包裝材料(鋁塑復合膜)進行封裝。軟包裝材料是軟包鋰電池中最關鍵、技術難度最高的材料。軟包裝材料通常分為三層,即外阻層(一般為尼龍 BOPA 或 PET 構成的外層保護 層)、阻透層(中間層鋁箔)和內層(多功能高阻隔層)。
軟包電池的包裝材料和結構使其擁有一系列優(yōu)勢,比如安全性能好,軟包電池在結構上采用鋁塑膜包裝,發(fā)生安全問題時,軟包電池一般會鼓氣裂開,而不像鋼殼或鋁殼電芯那樣發(fā)生爆炸;
重量輕,軟包電池重量較同等容量的鋼殼鋰電池輕40%,較鋁殼鋰電池輕20%;
內阻小,軟包電池的內阻較鋰電池小,可以極大的降低電池的自耗電;循環(huán)性能好,軟包電池的循環(huán)壽命更長,100次循環(huán)衰減比鋁殼少4%——7%;設計靈活,外形可變任意形狀,可以更薄,可根據客戶的需求定制,開發(fā)新的電芯型號。
軟包電池的不足之處是一致性較差,成本較高,容易發(fā)生漏液。然而,成本高可通過規(guī)?;a解決,漏液則可以通過提升鋁塑膜質量來解決。
隨著市場的進一步擴大和對續(xù)航里程要求的不斷提升,整車企業(yè)對動力電池在能量密度、制造成本、循環(huán)壽命和產品附加屬性等方面都提出了更高的要求。因此在 300 W·h/kg 項目中,將主要采用軟包作為封裝形式。
5.2 制備工藝
制備工藝主要有卷繞和疊片兩種形式。卷繞工藝下制備的電池(下文簡稱“卷繞式電池”)正負極通常只有單一極耳,而疊片工藝下制備的電池(以下簡稱“疊片式電池”)由于多個小極片并聯(lián),因而疊片工藝的內阻較低。
同樣由于極耳的差異,卷繞式電池倍率性能較差,難以大電流完成放電,而疊片電池倍率性能較好,更容易在短時間內完成大電流放電。
相似地,由于內阻高極化大,卷繞式電池一部分電壓被消耗于電池內部極化,因而其放電平臺略低。
而疊片式電池更接近材料的自身放電平臺。能量密度方面,由于體積比容量較低以及放電平臺 較低這兩個原因,致使卷繞式電池能量密度也不及疊片式電池。
厚度方面,由于卷繞式電芯內部結構不均一,極耳處、隔膜收尾處、電芯的兩邊都是容易超厚的位置,因而厚度難以控制。而疊片式電池,電芯內部結構一致,電池各個部位厚度也相應的一致,因此容易控制其厚度。
同樣的原因,由于卷繞式電池內部結構不均一,充放電時電芯內部反應程度、速率不均。
故對于較厚的卷繞電池而言,大倍率充放電后或者循環(huán)多次后,有變形的可能。而疊片式電池內部結構統(tǒng)一,反應速率相對一致,即使厚電芯也不容易變形。
電池形狀方面,卷繞式電池形狀單一,只能做成長方體電池。而疊片式電池尺寸靈活,可以根據電池尺寸來設計每個極片尺寸,從而可以做成任意形狀。
然而卷繞式電池操作方便。不論是人工卷繞還是半自動全自動卷繞,都可以較快速且高質量的完成,生產控制相對簡單。而疊片式電池操作復雜。
人工疊片費時費力;半自動或者全自動設備由于機械制造難度大門檻高又一時難以普及。其生產控制較繁瑣。每個電池有幾十個極片,檢測、轉運、統(tǒng)計等都是難點。兩種工藝間的比較簡單概括于表 1。

表1 卷繞和疊片工藝比較
由于疊片電池較高的能量密度及其它一系列優(yōu)點,為了實現(xiàn) 300W·h/kg 高能量密度電池體系,本項目最終采用疊片工藝進行電池制備。除了采用軟包封裝及疊片工藝外,在電池體系的設計時,還可以通過集流體減薄等方式實現(xiàn)電池的高能量密度。 06、整車 PACK
實現(xiàn)電池系統(tǒng)的高比能,在應用高能量密度電芯的同時,需要重點開展系統(tǒng)輕量化的研究工作。以科技部2017年新能源汽車試點專項對乘用車動力電池系統(tǒng)的要求,系統(tǒng)能量密度需要200 W·h/kg, 2018年指標則是210W·h/kg。
這意味著即使采用 300 W·h/kg 能量密度的電芯,系統(tǒng)的成組效率也要達到 66.7%——70%。即電芯在系統(tǒng)中重量比占7成左右,因此輕量化是電池系統(tǒng)開發(fā)的重點方向。圖 5 給出的是一款電池系統(tǒng)結構件的設計目標。
與目前電池系統(tǒng)相比,重點需要在箱體輕量化、模組機-電-熱一體化設計、液冷系統(tǒng)輕量化等多個方面開展工作。箱體輕量化方面,主要開展鋁合金、鎂合金等輕質有色金屬型材焊接成型、沖壓成型及壓鑄等工藝技術的開發(fā)驗證。
模組機-電-熱一體化設計方面,結合軟包電芯的實際應用環(huán)境,采用塑膠件+散熱鋁板一體化的模塊設計,保障模組剛度的同時,實現(xiàn)熱量的有效傳遞。液冷系統(tǒng)輕量化方面,逐步由鋁擠壓型材液冷板設計轉向了口琴管式 及吹塑成型式等輕質液冷板設計。
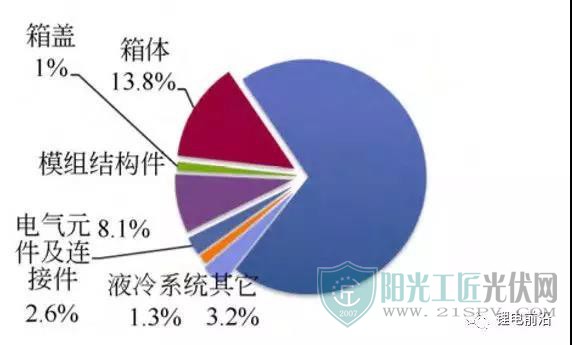
圖 5 電池系統(tǒng)結構件重量分配設計目標
安全性是動力電池系統(tǒng)應用的重中之重。一般來講,能量密度越高,其安全系數相對越低。特別是高比能量密度的三元電池熱失控時,其會噴發(fā)出高溫可燃氣體及高溫噴發(fā)物,同時產生起火燃燒的狀況。因此對于系統(tǒng)而言,如何保障電池單體發(fā)生熱失控后的系統(tǒng)安全性也是需要研究的重點。目前,電池系統(tǒng)熱失控的安全防護研究主要集中在: 首先,電池及模組間進行隔熱設計,有效延緩乃至阻止熱失控電池對相鄰電池及模組的加熱作用,同時結合液冷等高效散熱手段,保障相鄰電池及模組的熱平衡,使其保持在安全的溫度范圍;
其次,通過對電池失效因子(如CO等特征氣體)的檢測及合理的控制策略的設計,在電池熱失控前發(fā)出判斷預警,提升系統(tǒng)的安全性;
再次,可通過內置輕質滅火器,對電池熱失控產生的火焰進行有效的撲滅,降低系統(tǒng)失效風險。
最后,由于電池熱失控時會在短時間內噴出大量氣體,造成系統(tǒng)內壓急速升高,可設計相應的泄壓系統(tǒng),在保障電池系統(tǒng)有效泄壓的同時,排除高溫噴發(fā)物,降低對系統(tǒng)的加熱作用。
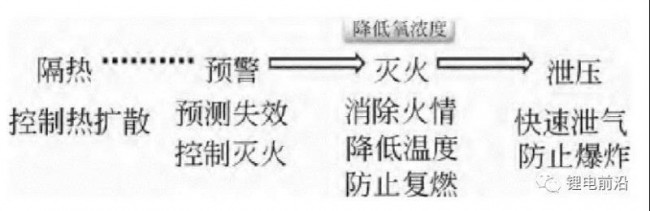
圖6 電池系統(tǒng)安全防護策略
07、BMS 主動均衡 作為新能源汽車ECU三大件之一的電池管理系統(tǒng)(BMS),其安全性已被完全納入整車 PACK 的安全性。BMS系統(tǒng)核心功能之一是利用均衡技術,包括主動均衡和被動均衡,消除電池組中單體電池的不一致性。對于高能量密度體系來說,電池的一致性顯得尤為重要。
在 PACK 大電流放電與充電的過程中,由于單體性能參數的不一致性,個別單體的發(fā)熱量較大,按照這種狀態(tài)的發(fā)展,單體的不一致性會進一步拉大。
在主動均衡技術的介入下,可以減小這些單體的放電與充電的電流,從而在一定意義上平衡整組PACK的熱場,進而可以最大限度地維持單體電池的一致性,延長PACK壽命。然而,區(qū)別于被動均衡技術,對主動均衡技術的各方面要求都比較高,具體表現(xiàn)如下。
① 主動均衡模式下,BMS 系統(tǒng)處于大電流的工作狀態(tài)下。大電流會導致電池包局部溫升過大,造成部分電池加速老化,嚴重時甚至導致PACK燃燒事故。
部分阻抗較高的元器件長期工作在較高的溫度下也會產生熱量,熱量聚集的結果就會導致溫升效應,也會使電池性能下降,甚至失效。
因此,主動均衡除了對單體電壓采集的精度有較高要求外,大電流對單體的影響也是需要考慮的重要問題?;谝陨戏治?,具有較低溫升及更高安全性的主動均衡產品是其未來發(fā)展的重要方向。
② 區(qū)別于被動均衡,主動均衡電路具有更高的復雜度,包括元器件的種類、數量、ASIC的功能。特別是對于一些具有特殊功能的ASIC和大功率的分立元器件,如果設計不當或者管控不嚴, 這些器件會大幅度降低產品的可靠性。
例如,在能量轉換電路中,大功率變壓器是能量轉換的中介,其性能的穩(wěn)定性對于產品的可靠性的重要性不言而喻。但此變壓器的缺點是重量大、韌性差,所以在劇烈的振動條件下,其較容易被損壞。低可靠性是限制主動均衡發(fā)展的又一重要因素。
③ 效率是主動均衡特有的屬性。從工作原理的角度上來說,區(qū)別于被動均衡,主動均衡是對單體能量進行轉移,在此轉移的過程中會有部分能量的損耗,能量損耗的占比就體現(xiàn)出了主動均衡效率的高低。
均衡過程中 能量損失的大小直接關系到整車的續(xù)航里程。從提 高整車續(xù)航里程的角度出發(fā),對于主動均衡,提高 均衡效率是其未來發(fā)展的又一重要方向。
④ 相比較被動均衡,主動均衡承載了更高級別的成本壓力,這也是近幾年來限制主動均衡發(fā)展的重要因素。為 了滿足整車廠對產品極高性價比的要求,在維持并滿足產品性能的同時,供應商也在激烈地打價格戰(zhàn)。低成本也是發(fā)展主動均衡 BMS產品的重要方向。
⑤ 從新能源整車的發(fā)展方向得知,電池 PACK包占整車質量與體積的比例需要越來越低。除了提高電池的能量密度與體積密度之外,BMS 的體積與質 量也同時需要被縮減。因而小型化也是主動均衡BMS產品的重要方向。
08、云平臺
除了構建高安全高性能的電池包之外,還可以通過云平臺實現(xiàn)設備遠程故障診斷分析、技術創(chuàng)新及節(jié)約效能等功能,不斷提高電池系統(tǒng)的應用水平。
通過構建統(tǒng)一的平臺,開放的系統(tǒng)架構和數據平臺,基于智能化、一體化構建面向企業(yè)的不同監(jiān)控數據應用、大數據分析應用。
云設備(IaaS)基礎設施作為服務(計算、存儲、網絡);軟件平臺 PaaS 作為中間件、應用服務器、數據庫的服務;應用SaaS作為應用、信息和數據服務。國軒遠程監(jiān)控平臺數據從2012年開始,已存儲5年的國軒電池運行數據,目前正在搭建包括生產、運營、售后及客戶關系的多方大數據云平臺。
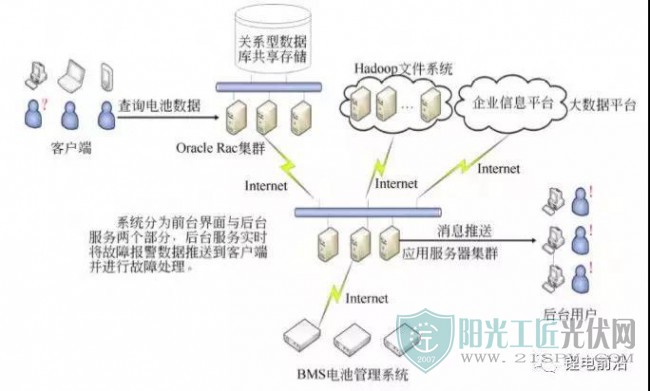
圖7 遠程監(jiān)控平臺系統(tǒng)架構圖
總結 動力電池是一個全方位的產品,做好動力電池性能的平衡也是一個系統(tǒng)性工程。材料的選型、化學體系的優(yōu)化是實現(xiàn)高能量密度的關鍵,但是電池的循環(huán)壽命和安全性能則受到影響,因此,必須從材料、隔膜、電解液以及電池結構設計等多方位優(yōu)化以提高電池循環(huán)性能,同時建立從材料、電池、模組到電池系統(tǒng)多級的防護措施以保證動力電池的安全可靠性……
本文來源:高安全高比能量動力鋰離子電池系統(tǒng)路線探索 合肥國軒高科動力能源有限公司 ;作者:曹勇,嚴長青,王義飛,李道聰,林少雄,梁大宇,代北北,胡攀攀,卞林,楊續(xù)來,徐興
原標題:解析國軒高科300wh/kg高鎳電池開發(fā)路徑