
使用減薄了的硅基板,采用背面電極的異質(zhì)結(jié)太陽能電池的制造工藝
用噴墨涂布方式形成了背面電極的蝕刻掩模(出處:福島大學(xué))
這是全球首例表面沒有電極且可自主彎曲的太陽能電池。因?yàn)橐子谠谇嫔显O(shè)置,所以有望應(yīng)用于建筑物、便攜式終端、汽車等廣泛用途。
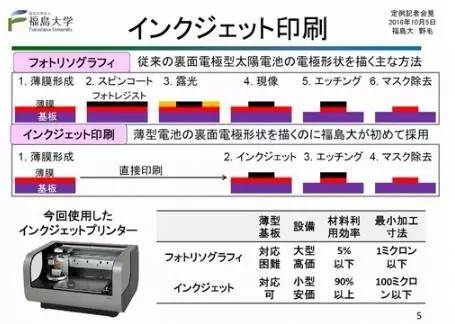
以噴涂簡化工藝。在形成蝕刻掩模時(shí)與光刻的差異(出處:福島大學(xué))
在這種價(jià)格低廉、輕薄且可彎曲的太陽能電池中,使用化合物或非晶硅制成的薄膜型太陽能電池比較知名,而使用硅基板的晶體硅型,將基板的厚度縮小到50μm(μm:微為百萬分之1)以下也能實(shí)現(xiàn)。
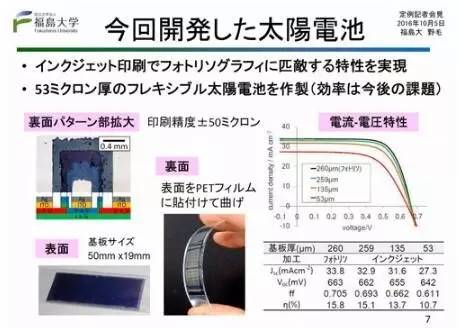
本次開發(fā)的太陽能電池(出處:福島大學(xué))
要進(jìn)一步提高晶體硅型太陽能電池轉(zhuǎn)化效率有兩個(gè)可行的方法,分別是異質(zhì)結(jié)和背面電極。福島大學(xué)對減薄厚度的晶體硅型太陽能電池就采用了這兩種方法。異質(zhì)結(jié)是將物性不同的半導(dǎo)體材料接合起來的技術(shù),把能將不同波長的光轉(zhuǎn)換為電的材料組合起來,可以提高轉(zhuǎn)換效率。
福島大學(xué)此次組合了晶體硅和非晶硅。將厚度為280μm的硅基板以研磨和蝕刻變薄,形成了異質(zhì)結(jié)型太陽能電池。加工后的總厚度約為53μm。
背面電極是只在太陽能電池的背面形成電極,并高效輸出電能的技術(shù)。一般的晶體硅型太陽能電池表面有電極,受光面積會因此而減少。將電極集中到背面,受光面變大,每個(gè)單元(發(fā)電元件)的轉(zhuǎn)換效率會提高。
用噴墨涂布方式形成背面電極。
現(xiàn)在背面電極的形成,采用的是半導(dǎo)體常用的光刻技術(shù),精度能達(dá)到±1μm以下。因?yàn)樵谛纬傻倪^程中,需要反復(fù)去除多余的膜,所以不僅工序復(fù)雜,材料的利用率也低至不到5%,而且每道工序都需要使用昂貴的制造裝置。
噴墨涂布與光刻相比,不僅可以大幅降低裝置的價(jià)格,還可使材料利用率達(dá)到90%以上。
此次,福島大學(xué)在光刻部分運(yùn)用噴墨涂布技術(shù),不但簡化了工序,還實(shí)現(xiàn)了太陽能電池所需要的±50μm的精度。
在形成特定膜之后,在上面噴涂了“掩模”,用來保護(hù)需要保留的部分。過去形成掩模的形狀需要經(jīng)過涂布光刻膠、曝光、顯影三道工序,而此次采用噴涂,只需要一道工序,就制作出了相同的形狀。
據(jù)稱,迄今沒有過由背面電極來減薄晶體硅型太陽能電池厚度的嘗試。這一方面是因?yàn)橛晒饪讨谱鞅趁骐姌O使用的制造裝置價(jià)格高昂,另一方面是因?yàn)榛鍦p薄后的問題。
在減薄之后,基板的機(jī)械負(fù)載會變?nèi)?。因此,在后續(xù)的制造工序中,會因?yàn)槭艿綑C(jī)械應(yīng)力而發(fā)生破損。
在此之前曾經(jīng)有兩個(gè)開發(fā)先例。二者都沒有采用硅基板,而是使用以氣體為原料形成(外延生長)的薄膜硅,并且接合了玻璃和硅制成的支持基板,以彌補(bǔ)機(jī)械強(qiáng)度的不足,使其能夠耐受生成電極等工序。
據(jù)稱,噴墨涂布的運(yùn)用也能防止減薄后的硅基板承受過大的機(jī)械載荷。此次,福島大學(xué)對減薄到大約53μm的硅基板直接進(jìn)行處理,成功形成了背面電極。
太陽能電池單元的尺寸約為10mm見方,3個(gè)單元排列在PET薄膜基板上,組成了50mm×19mm的太陽能電池模塊。
此次開發(fā)的電池轉(zhuǎn)化效率雖然只有10.7%,但通過改進(jìn)制造工藝等,設(shè)想可以提高到接近20%。
此為在文部科學(xué)省的地方創(chuàng)新戰(zhàn)略支援計(jì)劃“可再生能源先驅(qū)之地福島”中,在日本產(chǎn)業(yè)技術(shù)綜合研究所的協(xié)助下取得的研究成果,將在10月19~20日于BigPalette福島舉辦的“第5屆福島復(fù)興可再生能源產(chǎn)業(yè)展2016”上展示。