值得注意的是,包括SPS大軟包、麒麟電池、魔方電池都有著“共同”的特征:它們不再是傳統(tǒng)的從電芯到模組的簡單組合,它們是更具“靈活性”的系統(tǒng),因此將它們并列對比也更具價值。無疑,這些特征也意味著電池技術(shù)迭代趨勢。
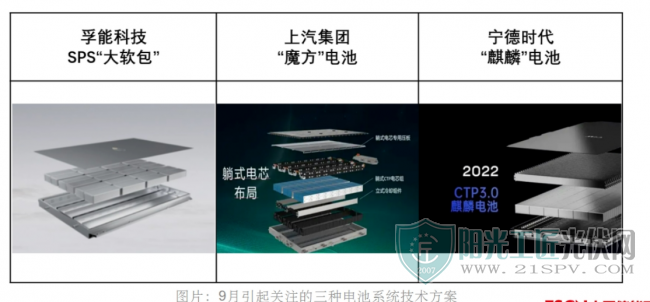
續(xù)航里程之爭,不止能量密度高低
對消費者而言,新能源汽車?yán)m(xù)航里程至關(guān)重要,而更遠的續(xù)航里程需要電池系統(tǒng)有著更高的能量密度相匹配。電池系統(tǒng)能量密度的提升通常有兩種方式:一是通過改善電池材料提升單體電芯能量密度;另一種途徑則是通過提升電池包系統(tǒng)集成度和體積利用率。當(dāng)然“成年人”的選擇是“全都要”,上述三種技術(shù)方案也都體現(xiàn)了這一點。
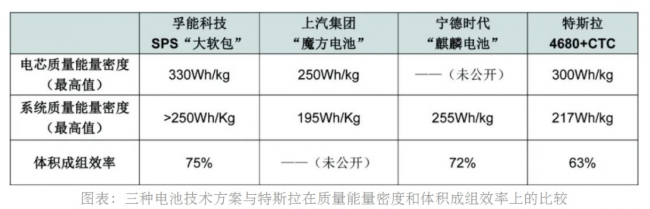
在電芯化學(xué)體系方面,三種技術(shù)方案都體現(xiàn)了高兼容度,可以適用從高鎳三元到低鎳富鋰錳、磷酸鐵鋰、甚至鈉離子等多種材料體系,這使得汽車廠商可以在一套方案中滿足成本和性能的不同取向。
其中,從單體能量密度來看,孚能科技采用獨有的半固態(tài)軟包電池技術(shù),已實現(xiàn)330Wh/kg的能量密度;寧德時代“麒麟電池”并未公布單體電芯,但是從其成組效率來看,預(yù)計也將達到300Wh/kg;特斯拉4680電池,能量密度也在300Wh/kg附近;上汽集團目前從市場采購的高鎳三元電芯能量密度在250Wh/kg左右。
在系統(tǒng)集成方面,三種技術(shù)方案均采用了“CTP”技術(shù)。其中孚能科技SPS方案采用液冷板與底盤一體化設(shè)計,半固態(tài)大軟包電芯直接集成于底盤系統(tǒng),使系統(tǒng)零部件減少50%,打破了軟包電池在系統(tǒng)集成度上的傳統(tǒng)劣勢;上汽的“魔方電池”最大的亮點在于躺式電芯,以及CTP、高電壓、超薄基材等技術(shù)及材料,也實現(xiàn)了成組效率上的極大突破;而寧德時代“麒麟電池”通過取消橫縱梁、水冷板、隔熱墊原本各自獨立的設(shè)計,集成為多功能彈性夾層,也實現(xiàn)了超出預(yù)期的模組集成度。
可以看到,通過“電池材料+系統(tǒng)高集成”雙管齊下的策略,電池企業(yè)、車企的技術(shù)方案都實現(xiàn)了電池系統(tǒng)能量密度的大幅提升,尤其是依托電芯化學(xué)體系方面的優(yōu)勢,孚能科技和寧德時代都可以為汽車廠商實現(xiàn)超過1000km的長續(xù)航里程。
通用化之爭,可調(diào)高度適應(yīng)多種平臺者勝
續(xù)航里程的提升只是一方面,孚能科技、特斯拉、寧德時代、上汽的新電池系統(tǒng)解決方案,都支持從A級到C級,支持轎車、SUV和MPV等多種平臺的適應(yīng)性,這也是今年這幾家企業(yè)電池系統(tǒng)解決方案的最大特征。必須看到,主流汽車廠商的電氣化進程正進入“架構(gòu)造車”的新時代。從過去的“油改電”,到專用電車平臺的“平臺造車”,再到適應(yīng)多個級別多種車型的“架構(gòu)造車”,這一趨勢也促使電池技術(shù)方案發(fā)生改變。

圖片:從MQB/J1,到MEB/PPE,再到SSP,大眾的平臺電氣化已走過三代
以孚能科技的SPS“大軟包”方案為例,其臥式布局和疊片技術(shù),可以靈活調(diào)節(jié)電池系統(tǒng)的底盤高度,即同款底盤、一款電芯就可以適配全系乘用車。具體來看,大軟包電芯厚度僅有14mm-20mm,可以通過不同的疊加方案實現(xiàn)不同的電芯厚度,而電芯厚度的變化讓SPS的底盤高度可以在85mm-145mm之間靈活調(diào)節(jié),搭載不同能量密度的大軟包電芯讓電池系統(tǒng)可擁有從80kWh-150kWh的不同容量,滿足從性能轎跑到城市皮卡的電動化需求。
上汽的“魔方”電池也是類似的表現(xiàn):其電池包的長度和寬度是固定的——1690mm*1300mm;而高度有三種:分別為110mm、125mm和137mm。不同的厚度適用于不同的車型定位,現(xiàn)有新能源轎車經(jīng)常出現(xiàn)的底盤過高導(dǎo)致乘員艙高度不足的問題將得到極大的緩解。
綜合可以看到,無論是上汽或大眾,都在強調(diào)電池系統(tǒng)提供統(tǒng)一底盤中的多個高度規(guī)格,以適用于多個平臺及多種車型,而這一“架構(gòu)造車”的理念正被越來越多的車企所采用。
安全及熱管理,電池廠和汽車廠各擅其場
在新的電池技術(shù)方案提升能量密度和通用化的同時,實現(xiàn)更好的熱管理及安全性依然是電池人的不懈追求。在三種技術(shù)方案中,SPS“大軟包”及“麒麟電池”,與“魔方電池”在系統(tǒng)結(jié)構(gòu)上表現(xiàn)出了更多的差異性,而這也是由電池廠和汽車廠對安全的不同理解與關(guān)注所決定的。

圖片:通過改變散熱結(jié)構(gòu),SPS和“麒麟”賦予電池更強的散熱效率,適應(yīng)更高的充能效率
孚能科技的SPS方案中,液冷板和導(dǎo)熱片的復(fù)合使用,給大軟包電芯提供了“雙面液冷,三面?zhèn)鳠?rdquo;的高效熱交換,電池系統(tǒng)的散熱效率提升4倍,加上精準(zhǔn)的控溫AI-BMS,電池系統(tǒng)循環(huán)壽命超過3000次。麒麟電池通過全新的多功能彈性夾層,以及重新設(shè)計置于側(cè)面而非頂部的水冷系統(tǒng),從而使換熱面積擴大4倍,電芯控溫時間縮短至原來的一半。可以看到,擴大散熱面積,滿足3C甚至4C的高壓充電是這兩種技術(shù)方案的主要訴求。
而上汽的“魔方”電池,則更強調(diào)避免產(chǎn)生熱失控的“骨牌”效應(yīng)。躺式電芯結(jié)構(gòu)下電池與電池間更小的接觸面積,再配合7*24h遠程監(jiān)控體系、提前散熱系統(tǒng)、氣凝膠阻燃材料、自動泄壓防爆閥等設(shè)計。這也體現(xiàn)了車企更加“系統(tǒng)化”的安全思路,通過撞不著、不失控、不連鎖,來實現(xiàn)最終的安全保證。
小結(jié):三種技術(shù)方案都能很好地滿足熱管理及安全,也都能通過針刺、擠壓等各類國標(biāo)安全測試。但必須看到一點,少電解液甚至無電解液的半固態(tài)及固態(tài)電池將改寫動力電池的安全性,而孚能科技是目前國內(nèi)率先推出半固態(tài)電池的企業(yè)。
寫在最后:成本管理成為一切制造的核心
盡管通過上面的數(shù)據(jù)梳理,我們可以比較和討論各種技術(shù)方案的優(yōu)劣性,但在現(xiàn)代制造業(yè)中,成本是另一個不容忽視甚至更重要的話題。在今年8月電池行業(yè)某次大會上,多家車企抱怨在為電池廠打,10月,一些車企開始積極自建電池產(chǎn)能,打破對電池廠的絕對依賴。但毫無疑問,追求更好的生產(chǎn)成本是新能源汽車進一步發(fā)展的必然之路,特斯拉通過圓柱電池、CTC和一體化壓鑄技術(shù)為行業(yè)樹立了一個很好的典范,而孚能科技的SPS大軟包墊片技術(shù),可能是另一種成本上的優(yōu)解,而這一點有待更多的車企來驗證。
原標(biāo)題: 從孚能科技SPS和寧德時代“麒麟電池”看電池系統(tǒng)迭代方向