氫氣(H2)來(lái)源廣泛,具有高能量密度、高轉(zhuǎn)化效率和清潔性的優(yōu)點(diǎn)。氫能作為零碳能源,是典型的二次能源,能源屬性類(lèi)似于電,在可儲(chǔ)存性方面優(yōu)于電。隨著社會(huì)和經(jīng)濟(jì)進(jìn)步,在人們對(duì)環(huán)保、效率、低碳能源的需求推動(dòng)下,氫能有望成為未來(lái)能源的重要構(gòu)成,在低碳社會(huì)中發(fā)揮重要作用。我國(guó)在氣候變化巴黎大會(huì)上承諾,將于2030年左右使二氧化碳(CO2)排放達(dá)到峰值,并爭(zhēng)取盡早實(shí)現(xiàn)2030年單位國(guó)內(nèi)生產(chǎn)總值 CO2排放比2005年下降60%~65%。要實(shí)現(xiàn)這個(gè)目標(biāo),離不開(kāi)氫能的減排貢獻(xiàn)。根據(jù)國(guó)際氫能委員會(huì)預(yù)測(cè),到2050年,氫能將減少 CO2排放60億噸,創(chuàng)造2.5萬(wàn)億美元的市場(chǎng)價(jià)值,在全球能源中所占比重有望達(dá)到18%。與傳統(tǒng)石油燃料易運(yùn)輸、可規(guī)模儲(chǔ)存的特點(diǎn)不同,目前氫儲(chǔ)運(yùn)技術(shù)尚未解決能效性、安全性等問(wèn)題,而且廣泛采用的高壓氣氫運(yùn)輸存在儲(chǔ)氫密度低、壓縮能耗高等問(wèn)題,無(wú)法大規(guī)模遠(yuǎn)距離運(yùn)輸。目前正在研發(fā)的儲(chǔ)氫方式有液氫、固態(tài)儲(chǔ)氫、有機(jī)液體儲(chǔ)氫和氨/甲醇儲(chǔ)氫。
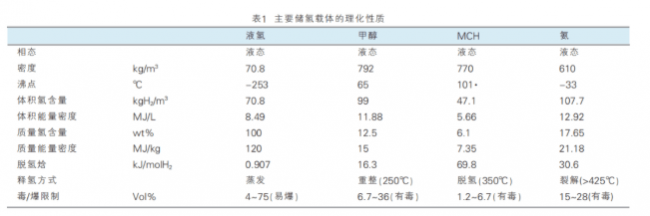
2020年全球氨產(chǎn)量約為1.83億噸,其中約1/4由中國(guó)生產(chǎn),另外30%來(lái)自俄羅斯、美國(guó)和印度。在氨總產(chǎn)量中,72%來(lái)自天然氣,22%來(lái)自煤炭,5%來(lái)自石油,只有不到1%來(lái)自可再生能源。其全部產(chǎn)能的80%用于生產(chǎn)化肥,其余用于生產(chǎn)炸藥和化工品。由于傳統(tǒng)合成氨的制氫單元需要消耗大量的化石能源,會(huì)產(chǎn)生大量 CO2,因此通過(guò)電解水生產(chǎn)綠氫,并通過(guò)H-B工藝將其合成氨,被認(rèn)為是低碳合成氨路線(xiàn),所生產(chǎn)的氨被定義為“綠氨”,是綠氫載體。但將氫轉(zhuǎn)化為氨需要的能量相當(dāng)于氫所含能量7%~18%,如果氨需要在目的地重新轉(zhuǎn)化為氫氣,在有催化劑的條件下需要500~550℃的熱源,又會(huì)造成一部分能量損失。
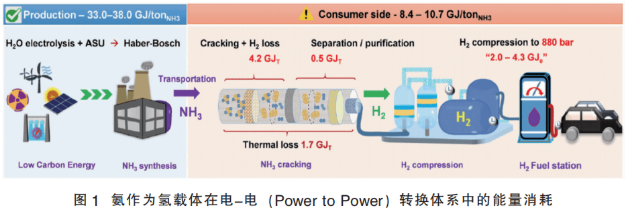
目前綠氫主要通過(guò)可再生電源電解水獲得。電解水的主要設(shè)備是電解槽,目前主流的電解槽是堿性電解槽和PEM電解槽。雖然堿性電解槽成本低廉,但由于其電流密度低、體積大,在大規(guī)模制氫條件下不具備優(yōu)勢(shì)。PEM電解槽因高效率、長(zhǎng)壽命、高電流密度而被認(rèn)為更適用于大規(guī)模氫氣生產(chǎn)。一般來(lái)說(shuō),電解槽需要的理論最小值為21.18 GJ/噸氨。然而,在工業(yè)規(guī)模上,電解槽的運(yùn)行效率為60%~70%,至少需要30.3~35.3GJ/噸氨。此外,當(dāng)前通過(guò)空氣分離裝置生產(chǎn)氮?dú)庀募s2.7 GJ/噸氨。因此在理想條件下,通過(guò)該途徑生產(chǎn)的氨能耗為33.0~38.0GJ/噸氨,整體動(dòng)力燃料(PTF)效率為55.7%~64.3%(表2)。相比之下,液氫由于在壓縮和液化過(guò)程中需要36.0~48.0 GJ/噸H2能量,液氫的PTF(Power to Fuel Cell)效率為49.3%~57.9%,低于氨。此外,由于蒸發(fā)損失和壓縮存儲(chǔ)的能耗較高,液氫的運(yùn)輸效率約為84%,低于氨(90%)。
將氨應(yīng)用于燃料電池有兩條路徑。一是將氨催化裂化以產(chǎn)生用于燃料電池的氫氣。由于直接車(chē)載裂解需要提高車(chē)載系統(tǒng)的復(fù)雜度和集成度,抬高了成本,被認(rèn)為不切實(shí)際,因此該路線(xiàn)未來(lái)可能主要用于加氫站,即加氫站通過(guò)氨在線(xiàn)裂解制氫(圖1)。裂解過(guò)程需要>500°C的高溫才能生產(chǎn)高純度氫氣(>99.97%,特別是用于汽車(chē)),這需要4.2 GJ/噸氨(包括 H2損失)能量輸入。由于PEMFC極易受到微量氨的影響(<0.1×10-6),因此氨轉(zhuǎn)化的氫氣必須通過(guò)高效的純化和分離系統(tǒng)進(jìn)行精華提純,這將額外消耗0.5 GJ/噸氨。因此,氨分解氫氣的純化過(guò)程不可避免地產(chǎn)生大量成本。同時(shí),整個(gè)過(guò)程還可能導(dǎo)致1.7 GJ/噸氨的總熱損失。此外,氨分解后,還需要2.0~4.3GJ/噸氨的額外電能將氫氣壓縮,以重新填充燃料電池汽車(chē)(FCEV)700bar的儲(chǔ)氫瓶。通說(shuō)上述計(jì)算,氨的總轉(zhuǎn)化效率為61.0%~68.5%。此外,裂化反應(yīng)器與氫氣壓縮系統(tǒng)的集成可能會(huì)使燃料加注和填充過(guò)程復(fù)雜化。由于裂化系統(tǒng)的復(fù)雜性,以及在雜質(zhì)存在下催化劑的性能和壽命,可能會(huì)進(jìn)一步限制氨的應(yīng)用。
另一途徑是直接利用氨,不再需要中間過(guò)程將氨轉(zhuǎn)化為氫氣。未來(lái)可以利用SOFC內(nèi)部的高溫將氨裂解。然而,SOFC的高運(yùn)行溫度(550~900°C)可能僅適用于無(wú)需頻繁開(kāi)關(guān)的連續(xù)固定應(yīng)用。因此,SOFC可應(yīng)用于重型載具,例如用于航空、航運(yùn)、卡車(chē)運(yùn)輸?shù)取4送?,?fù)責(zé)將氨催化分解為氫氣的SOFC陽(yáng)極材料在連續(xù)運(yùn)行過(guò)程中應(yīng)該具備穩(wěn)定、耐用和耐高溫特性,但目前陽(yáng)極材料的退化仍然是SOFC商業(yè)化的主要障礙。最近,Minutillo等人提出了一種基于以氨為燃料的SOFC技術(shù)的新型工廠(chǎng)配置,用于在加氫站現(xiàn)場(chǎng)制氫時(shí)同步生產(chǎn)電力。進(jìn)一步改進(jìn)SOFC和氨分解技術(shù)對(duì)于實(shí)現(xiàn)這樣的概念是必要的。氨內(nèi)燃機(jī)雖然不需要從氨中還原氫氣,但除了會(huì)產(chǎn)生NOx排放外,還可能導(dǎo)致諸如點(diǎn)火困難、火焰速度低、壓縮率更高等其他問(wèn)題。
雖然以上討論基于理想的燃料生產(chǎn)效率和實(shí)際運(yùn)輸分析,但氨作為可行的氫儲(chǔ)能材料確實(shí)具有巨大潛力。但與液氫相比,使用氨作為氫載體的運(yùn)輸體系在整體的電-燃料-電(PFP)效率方面沒(méi)有明顯優(yōu)勢(shì)(表 2)。另外,裂解過(guò)程對(duì)大量能量的需求限制了其未來(lái)的應(yīng)用。此外,凈化和壓縮后的氫氣用于供應(yīng)燃料電池汽車(chē)的財(cái)務(wù)和能源成本都很高,其中投入的電能和熱能成本難以通過(guò)其他方面的收益回收。除了其技術(shù)挑戰(zhàn)外,氨的毒性(OSHA暴露限值為50 ×10-6)、親水性和腐蝕性也需要大量基礎(chǔ)設(shè)施,以避免意外泄露和設(shè)備腐蝕。一般認(rèn)為,氨可以作為固定發(fā)電的燃料,使用SOFC為偏遠(yuǎn)地區(qū)供電。但作為氫載體,雖然其能量密度高,但還原氫氣需要大量的能量以裂解和壓縮,限制了它的應(yīng)用。從應(yīng)對(duì)氣候變化的角度看,采用以綠氫為原料來(lái)合成氨,替代傳統(tǒng)以化石能源為原料的合成氨工藝,是比采用氨作為氫載體更為有效的方法。
原標(biāo)題:氨作為氫載體,在氫能交通領(lǐng)域具有哪些優(yōu)勢(shì)與劣勢(shì)?